Our tool for managing your permission to our use of cookies is temporarily offline. Therefore some functionality is missing.

BMW ON THE WAY TO A SUSTAINABLE FUTURE.
DISCOVER HOW THE BMW GROUP IS COMMITTED TO SUSTAINABLE MOBILITY.
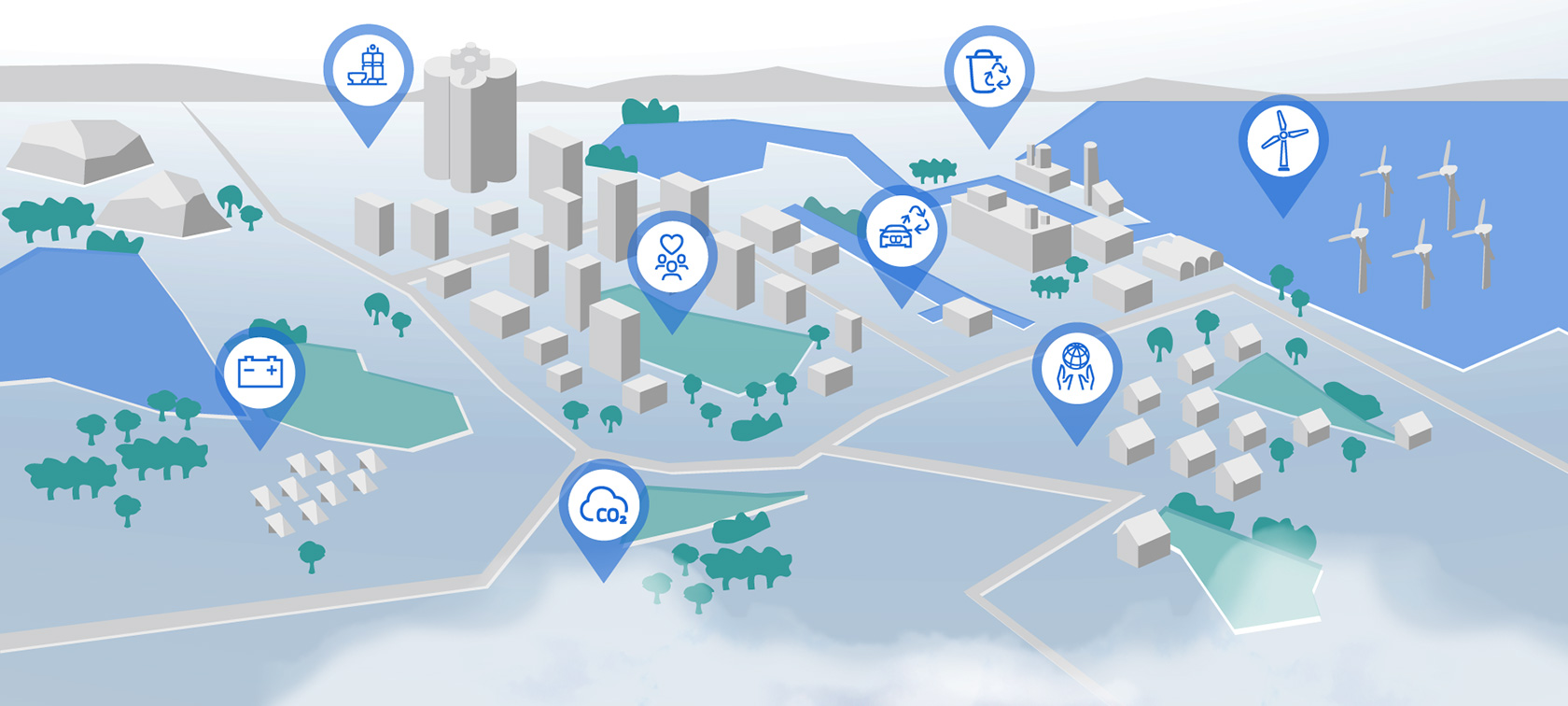
1. ELECTRIFIED MOBILITY.
The BMW Group has already put 1,000,000 electrified vehicles onto the road by 2021.
2. BATTERY RECYCLING.
90% of the materials in the high-voltage battery in an electrified vehicle from the BMW Group are recyclable.
3. INCLUSION.
6.5% of the people who work for the BMW Group have a disability – after all dedication recognises no differences.
4. CIRCULAR APPROACH.
60 kg of recycled plastics on average are integrated into a new BMW Group vehicle – this represents a proportion of up to 20%.
5. WASTE PROCESSING.
99% of the waste generated from our worldwide internal production of 2.5 million vehicles per annum is, in the year 2021, either recycled as materials (93.4%) or undergoes further (e.g., thermal) processing (5.8%).
6. ENERGY-SAVING MEASURES.
130 million kWh of electricity are being saved by the BMW Group yearly since 2018 thanks to switching over to LED lighting in 16 plants.
7. DIVERSITY.
The 120,000 colleagues who work for the BMW Group come from 113 nations – diversity is one of our key success factors.
8. REDUCED CO2 EMISSIONS.
A 78.1% reduction in the emissions generated during the production of every vehicle from the BMW Group has been achieved during the period between 2006 and 2022.
VEHICLES & MATERIALS.
OUR PATH TO MORE SUSTAINABILITY SHOWN BY THE NEW BMW iX.
Find out how the BMW iX perfectly combines innovation and luxury. By clicking on “Shop The Look“, you can continue to configure the BMW iX presented in the video to match your wishes.
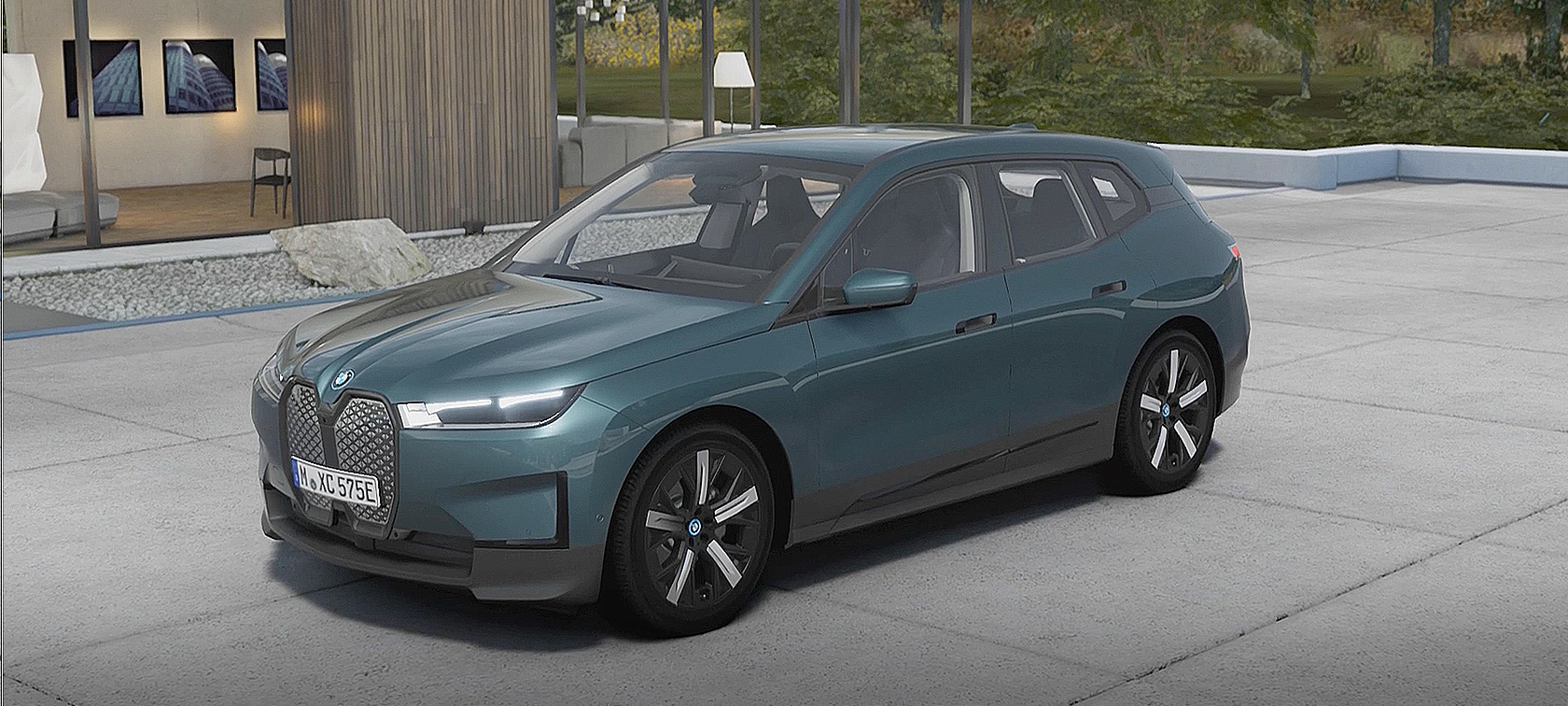
ELECTRIFIED DRIVING PLEASURE IN ITS MOST SUSTAINABLE FORM.
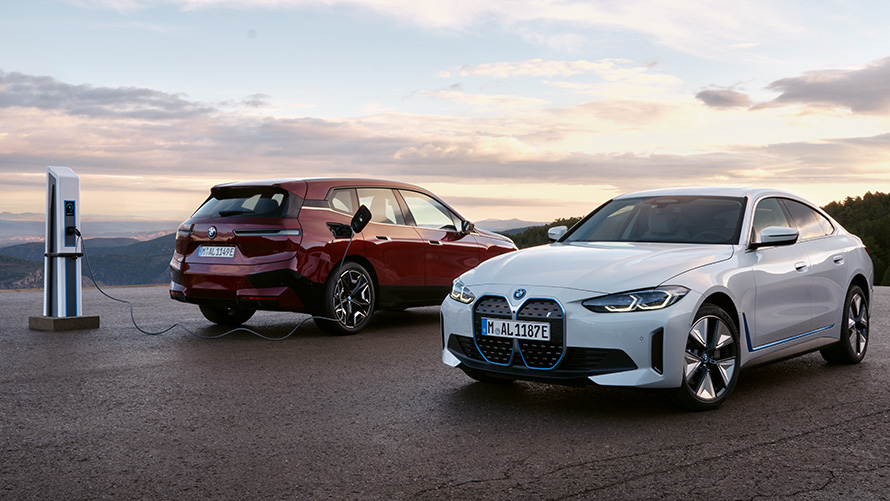
RECYCLED MATERIALS – REUSE OVER DISPOSAL.

Fishing nets.
The floor panels in the BMW iX and in the new BMW X1 are made from a plastic thread that takes disused fishing nets, floor coverings and scrap from plastics production as its starting materials. A new and still unique recycling process will in future convert fishing nets and lines into a high-quality recycled plastic that will be put to use in the New Class as of 2025. The panelling parts used on the inside and outside result in 25% fewer CO2 emissions than conventionally produced components.

Plastics recycling.
Recycled materials are used in many components of a BMW. Examples include the guides for the bumpers, the substructure of the door panels, the windscreen panel cover and the frame of the front cowling of the BMW iX which are all produced 100% from recycled plastic.

Cactus fibres.
In cooperation with start-up companies, the BMW Group is developing innovative bio-based surfaces. The newly developed Deserttex™, for instance, is made up of pulverised cactus fibres and a bio-based polyurethane matrix. In this way, the avoidance of animal-based products can be combined with a significant reduction in CO2.
MORE SUSTAINABLE AUTOMOTIVE PAINTS MADE FROM BIOMASS.
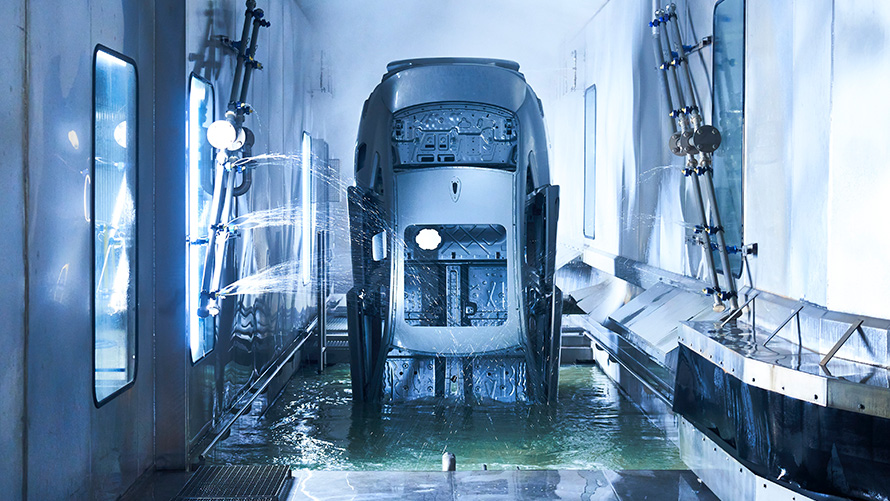
The paint shops in the European BMW Group plants use matt-finish paints that are not produced from crude oil, but instead from regenerative raw materials such as biological waste. In addition, the BMW Group plants in Rosslyn and Leipzig also employ sustainably produced anti-corrosive coating. The CO2 reductions in a process certified by TÜV amount to more than 15,000 tonnes in the period 2022 to 2030.
FREQUENTLY ASKED QUESTIONS ON THE TOPIC OF VEHICLES & MATERIALS.
How sustainable are electric cars?
The CO2 footprint of the fully electric BMW iX3, for example, is 30% more favourable than a BMW X3 sDrive20d taken as reference vehicle when the average electricity available on the European market is used (based on a consumption in line with the statutory WLTP cycle). If the battery is exclusively charged with electricity from renewable energies, the savings in CO2 emissions even rise to 60%.
How long does the battery of an electric car last?
The BMW Group has the experience of more than 1 million electrified models in the last 10 years. Therefore, when you purchase a new BMW plug-in hybrid and BMW i electric vehicle, you will receive an extended warranty for the high-voltage storage system with a maximum mileage of up to 160,000 km.
What are the constituents of the battery in an electric car?
A lithium-ion battery comprises the four components of cathode, anode, separator and electrolyte. Key factors in the quality of the battery are the precise quantities and in turn the quality of the constituent parts – but also how the individual components are combined and processed.
What future-oriented materials are used in the vehicles from BMW?
Through the use of regenerative raw materials and natural fibres, recycled plastics, vegan alternatives to leather as well as recyclable textiles, the BMW Group is aiming to heighten general awareness of sustainable materials and offer transparent insight into its path towards a sustainable future.
From the viewpoint of the BMW Group, only a holistic approach in dealing with established and new materials will be able to sustainably reduce CO2 emissions in the long run. For this reason, the BMW Group is not only accelerating the successful development of a market for secondary materials but is also intensifying the collaboration with innovative start-ups in the field of future-oriented materials.
What is BMW doing for the recycling of electric car batteries?
Under the heading “Design for Recycling”, the BMW Group sees the development and production of every new BMW vehicle as laying the foundations for an environmentally compatible method of recycling. This also includes end-of-life high-voltage batteries in electric vehicles. In addition to a secondary usage as stationary electricity storage for stabilising the public electricity grid, the BMW Group is also working with various partners to develop recycling and the establishment of closed material cycles (circularity) for battery cells.
CIRCULARITY & RESOURCES.
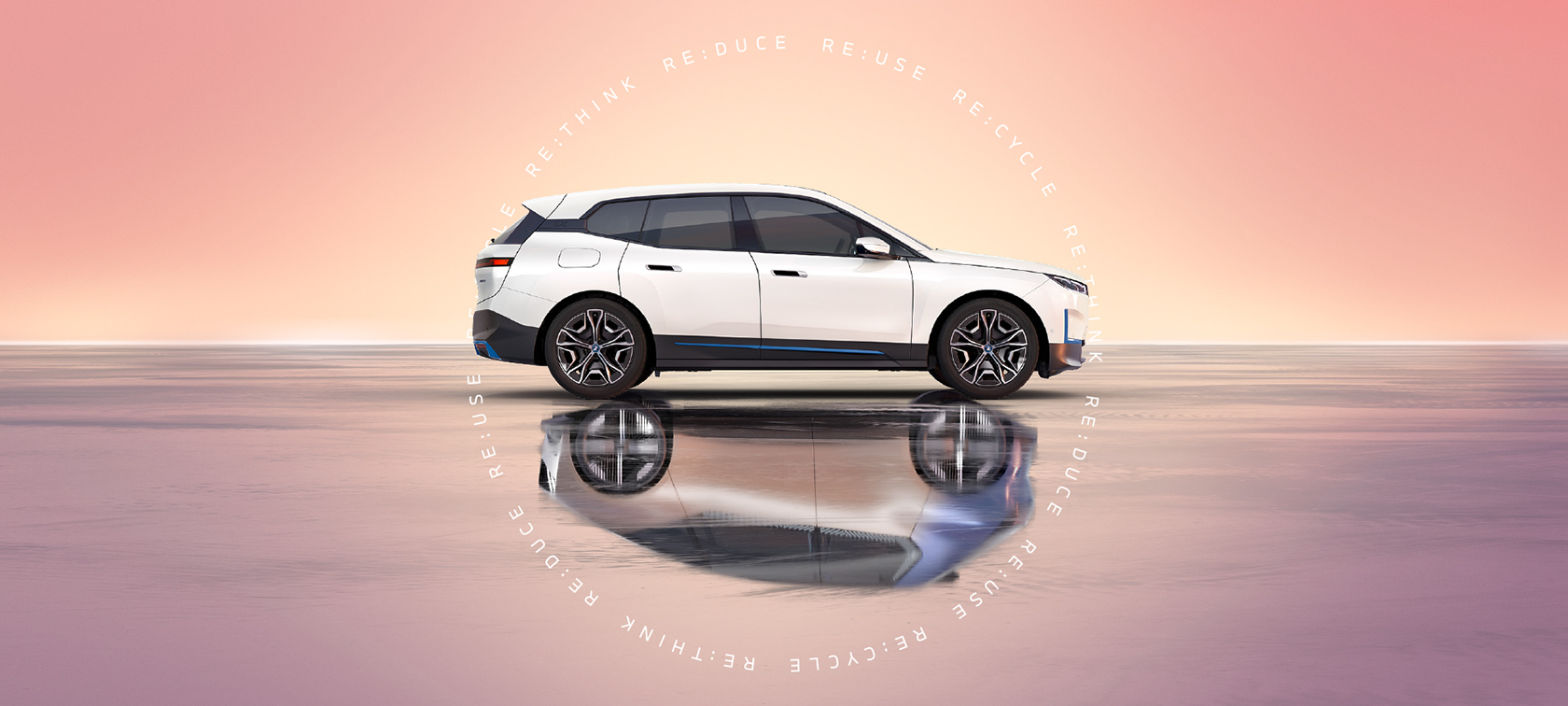
DISCOVER THE POWER OF CIRCULARITY.
OUR VISION: BUILDING THE CARS OF TOMORROW FROM THOSE OF TODAY.
The responsible handling of resources plays a key role for the BMW Group. In this process, we wish to continue using raw materials in line with our four principles of the circular economy:
RE:THINK – Creating with circularity in mind is everything we do
RE:DUCE – Doing more with less wherever we can
RE:USE – Extending the value of our products as much as we can
RE:CYCLE – Keeping resources in the loop as long as we can
THE FOUR PHASES IN THE LIFE OF A BATTERY CELL.

Development.
In the Cell Manufacturing Competence Centre in Munich, the BMW Group is conducting research into the ideal chemical composition for the cells in a lithium-ion battery cell. This involves subjecting the constituent parts of cathode, anode, separator and electrolyte to a sophisticated development process.

Use in vehicle.
Today’s electric vehicles already achieve a range in excess of 600 km with one charge, and the trend is rising. Experience shows that electric vehicles are able to achieve the same mileage as their conventional counterparts without any need to exchange the high-voltage battery.

Second Life.
Following intensive use of the lithium-ion battery in the vehicle, it would be possible to continue deploying it for many years to come as stationary storage in battery farms, for example, before it enters the recycling process.

Recycling.
The raw materials of the battery cell can be reprocessed. In the Cell Manufacturing Competence Centre, the BMW Group is developing the recycling of secondary raw materials for the next generation of battery cells. This marks the end of the life cycle for the battery cell – and it can then start all over again.
WIND, SUN AND INNOVATIVE TECHNOLOGIES.
TWO PLANTS. TWO EXAMPLES.

Wind energy.
The four wind turbines on the grounds of the BMW Group plant in Leipzig are each able to achieve a nominal output of 2.5 MW. They cover about one eighth of the electricity required in the plant. An intelligent storage farm in which up to 700 BMW i3 batteries are linked in a network stores surplus energy from the four wind turbines in times of surplus supply and feeds the electricity back into the grid when there is insufficient wind.

Solar energy.
The solar power plant in the BMW Brilliance Automotive Ltd. Plant Dadong (Shenyang) is able to produce more than 21 MWh of renewable energy in 2022. To this end, its area has been increased by 110,000 m2 – equivalent to roughly 15 football pitches – to a total of 290,000 m2 during the course of the Shenyang site expansion.
FREQUENTLY ASKED QUESTIONS ON THE TOPIC OF CIRCULARITY & RESOURCES.
What does circular economy mean?
Circular economy – also called circularity – refers to the principle that products are reused for new products or materials after their initial use as a raw material.
Why is the circular economy important?
Protecting and maintaining the environment, using valuable resources multiple times and ensuring that less waste is generated – this is what the BMW Group is pursuing with its four principles of the circular economy. In addition, the use of secondary materials (e.g. aluminium) enables CO2 reductions to be achieved. Innovation is the key to achieving a circular economy.
Which energy sources does BMW use?
The BMW Group plants are continuously promoting environmental protection through transformation with a focus on sustainability and the use of renewable materials. We employ the most effective measure according to the prevailing conditions and location. This ranges from regional green electricity from hydropower, such as in the BMW Group plants in Munich and Dingolfing, via electricity generation from photovoltaic plants in the Chinese BBA plants in Shenyang and a biogas plant some 100 km from the South African BMW Group plant in Rosslyn, through to electricity production from wind energy in the BMW Group plant Leipzig.
PRODUCTION & SUPPLY CHAIN.
MEASURES FOR MORE SUSTAINABILITY AT BMW PRODUCTION SITES.
A focus on sustainability and customer proximity is what distinguishes the BMW Group. This is why we produce directly on site all over the globe while maintaining uniform quality and safety standards.
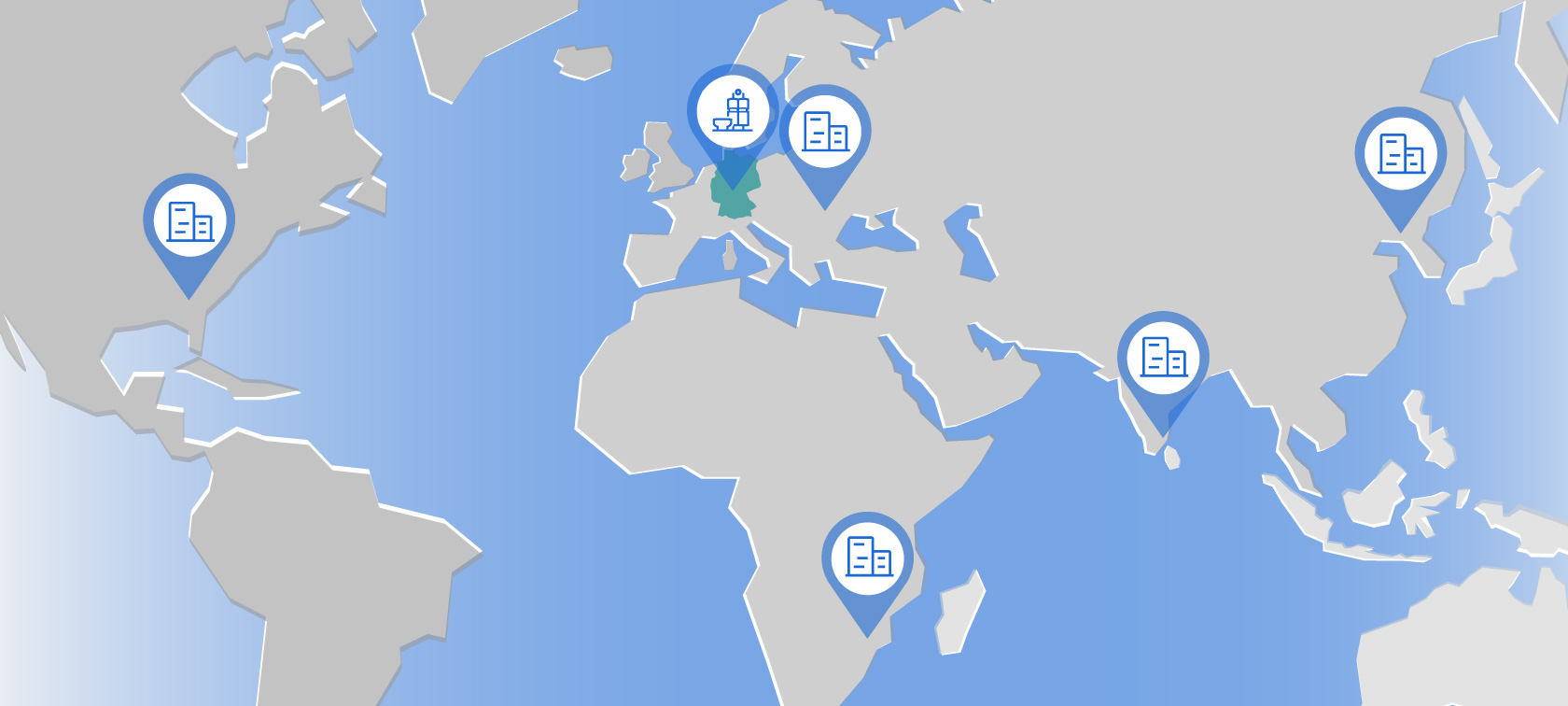
GERMANY.
Munich: A reverse osmosis plant is used to process wastewater from cathodic dip coating – a kind of primer application for vehicles – and reuses the wastewater in the same process step. In total this reduces annual freshwater consumption by more than six million litres. The green roof of the paint shop with its area of some 10,000 m2 not only improves insulation but also the air quality on site.
Dingolfing: Thanks to a combined heat and power plant, the BMW Group Plant Dingolfing produces almost half of its own electricity demand. From external procurement, 100% green electricity is used, which also includes green electricity obtained directly from local hydroelectric power stations. The plant meets more than 40% of its water requirements through its own wells, thus preserving the region’s drinking water reserves.
Leipzig: A smart battery farm stores surplus energy from the four wind turbines in times of surplus supply and feeds the electricity back into the grid when there is no wind.
DADONG (CHINA).
In addition to its solar facilities covering an area of some 110,000 m2, the BMW Brilliance Automotive Ltd. Plant Dadong (Shenyang) segregates its aluminium and steel scrap and does not use any freshwater in the painting process. The in-company train station also enables 80% of the finished vehicles to be transported entirely or partly to their respective destinations by rail.
ROSSLYN (SOUTH AFRICA).
The BMW Group Plant Rosslyn obtains its electricity from a biogas plant linked to a large beef cattle farm situated approximately 100 km away. Dung from the roughly 30,000 animals supplies up to 30% of the local power requirement. Furthermore, the paint shop – like its counterpart in Leipzig – uses sustainably produced anti-corrosive coating, which reduces CO2 emissions by 40% compared with coatings from fossil-based sources.
1. SPARTANBURG (USA).
The BMW Group Plant Spartanburg uses the methane gas from the neighbouring landfill site to meet up to 25% of its own energy demand by means of a combined heat and power plant. Every year, 400 solar modules produce a further 135 MWh of green electricity.
2. GERMANY.
Munich: A reverse osmosis plant is used to process wastewater from cathodic dip coating – a kind of primer application for vehicles – and reuses the wastewater in the same process step. In total this reduces annual freshwater consumption by more than six million litres. The green roof of the paint shop with its area of some 10,000 m2 not only improves insulation but also the air quality on site.
Dingolfing: Thanks to a combined heat and power plant, the BMW Group Plant Dingolfing produces almost half of its own electricity demand. From external procurement, 100% green electricity is used, which also includes green electricity obtained directly from local hydroelectric power stations. The plant meets more than 40% of its water requirements through its own wells, thus preserving the region’s drinking water reserves.
Leipzig: A smart battery farm stores surplus energy from the four wind turbines in times of surplus supply and feeds the electricity back into the grid when there is no wind.
3. DEBRECEN (HUNGARY).
The new BMW Group Plant under development in Debrecen represents the world’s first automobile plant to completely avoid the use of fossil-based energy sources in its vehicle production.
4. DADONG (CHINA).
In addition to its solar facilities covering an area of some 110,000 m2, the BMW Brilliance Automotive Ltd. Plant Dadong (Shenyang) segregates its aluminium and steel scrap and does not use any freshwater in the painting process. The in-company train station also enables 80% of the finished vehicles to be transported entirely or partly to their respective destinations by rail.
5. CHENNAI (INDIA).
In 2021, the BMW Group Plant Chennai collected some 13 million litres of rainwater – and was thus able to meet roughly 90% of its annual water demand. During the same period, the plant’s solar facility supplied more than 60% of energy needs.
6. ROSSLYN (SOUTH AFRICA).
The BMW Group Plant Rosslyn obtains its electricity from a biogas plant linked to a large beef cattle farm situated approximately 100 km away. Dung from the roughly 30,000 animals supplies up to 30% of the local power requirement. Furthermore, the paint shop – like its counterpart in Leipzig – uses sustainably produced anti-corrosive coating, which reduces CO2 emissions by 40% compared with coatings from fossil-based sources.
BMW TAKES RESPONSIBILITY.
Sustainability covers many aspects at BMW: from the inspection of our supply chains through to support for external programmes, we do everything to keep our ecological footprint as small as possible.
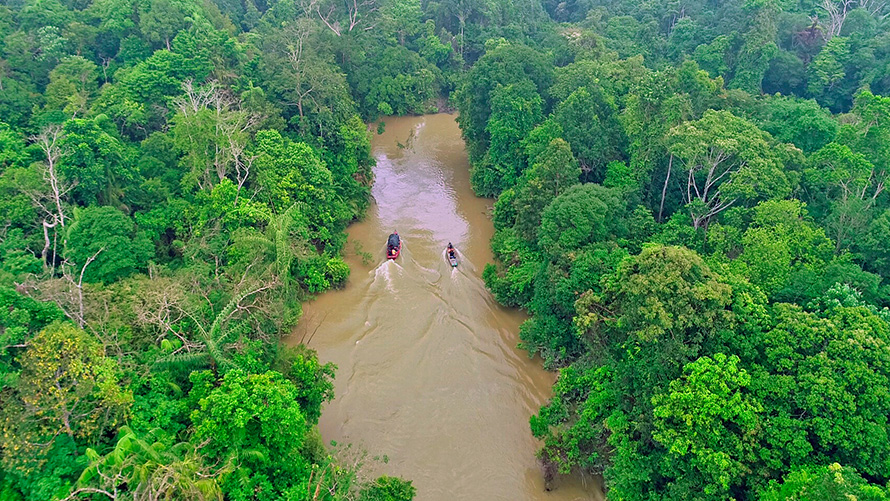
Sustainability programmes.
The BMW Group is the first German automobile producer to join “Business Ambition for 1.5 °C”. This includes our commitment to climate neutrality along the value-added chain until 2050. As a consequence, we are automatically a member of the UN “Race to Zero” programme. On the other hand, our long-standing membership of the “United Nations Environmental Programme” is yet another indication of how seriously the BMW Group takes sustainability.
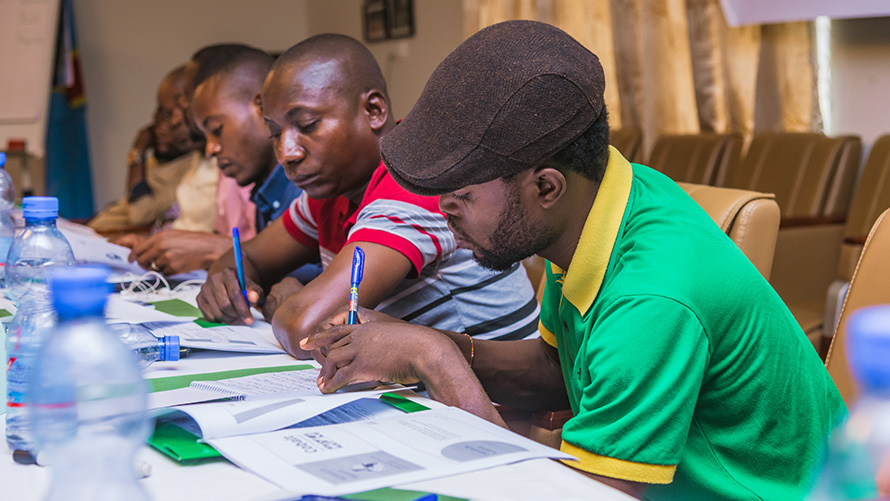
Cobalt for Development.
The BMW Group seeks to bring cobalt mining and processing in line with its sustainability and internationally applicable labour standards. To this end, the BMW Group, together with a number of other partners, established 2018 the cross-industry initiative Cobalt for Development in order to improve the labour and living conditions of workers in small-scale cobalt mining in the Democratic Republic of Congo.
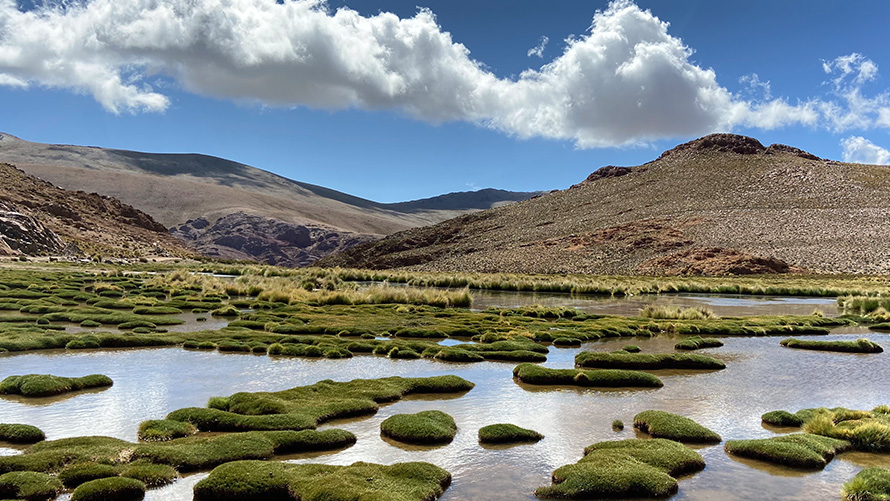
Supply chain management and logistics.
A multi-stage process secures our responsibility for the supplier network within all relevant divisions of the BMW group. Among the divisions in which we have introduced specifications for social and environmental standards are energy usage, logistics and the development of components, as well as in the contract-awarding process as a decision-making criterion as well as in supplier development. In order to implement these environmental and social standards, we are co-creators of the Responsible Supply Chain Initiative (RSCI) founded for this purpose and today we are already relying on electric trucks to supply the plants in some cases and are supporting initiatives aimed at organising the sea transport of vehicles to generate fewer emissions.
FREQUENTLY ASKED QUESTIONS ON THE TOPIC OF PRODUCTION & SUPPLY CHAIN.
What measures does the BMW Group implement in raw materials procurement?
Securing the adherence to environmental and social standards in the supplier network is the declared aim of the BMW Group. This particularly includes observing human rights and the sustainable extraction of raw materials. Potential risks arise above all in the production and subsequent processing of 37 raw materials and groups of materials that are relevant for us. Examples include natural rubber, tungsten, lithium and cobalt. We confront these risks with standardised, preventive and reactive measures tailored to each raw material, as well as with measures specific to the BMW Group.
What sustainability standards apply to BMW suppliers?
The BMW Group applies a large number of measures to ensure environmental and social standards within the supplier network. BMW expects all suppliers to implement an effective programme of environmental protection management, to adhere to environmental standards and to continuously minimise resource consumption and environmental impacts (energy, water, waste, emissions, etc.). Various actions, such as audits, are employed to monitor compliance.
What are CO2 emissions?
CO2 emissions occur, for example, due to the combustion of carbonaceous materials such as oil, coal and wood. Consequently, the quantity of CO2 emissions has risen tremendously since industrialisation. The originators of CO2 emissions are producers of electricity and heat as well as industry but also private households. With respect to the automotive industry, CO2 emissions can result from the production, use and disposal of vehicles. This is why the BMW Group is attempting to address all three issues in order to reduce CO2 emissions.
How does BMW help me to reduce my CO2 footprint?
Changing over to an electrified BMW model can reduce the individual CO2 footprint during the use phase compared with a vehicle fitted with a classic combustion engine. Technologies such as eDrive Zones additionally help to realise the full potential of a BMW plug-in hybrid. Furthermore, the My BMW App [digital solutions to support your e-mobility] offers smart services for a driving style that conserves resources.
SOCIAL & GOVERNANCE.
FIND OUT MORE – WITH THE BMW PODCASTS.
Experience fascinating new ideas for sustainability at BMW with the podcasts from our employees.
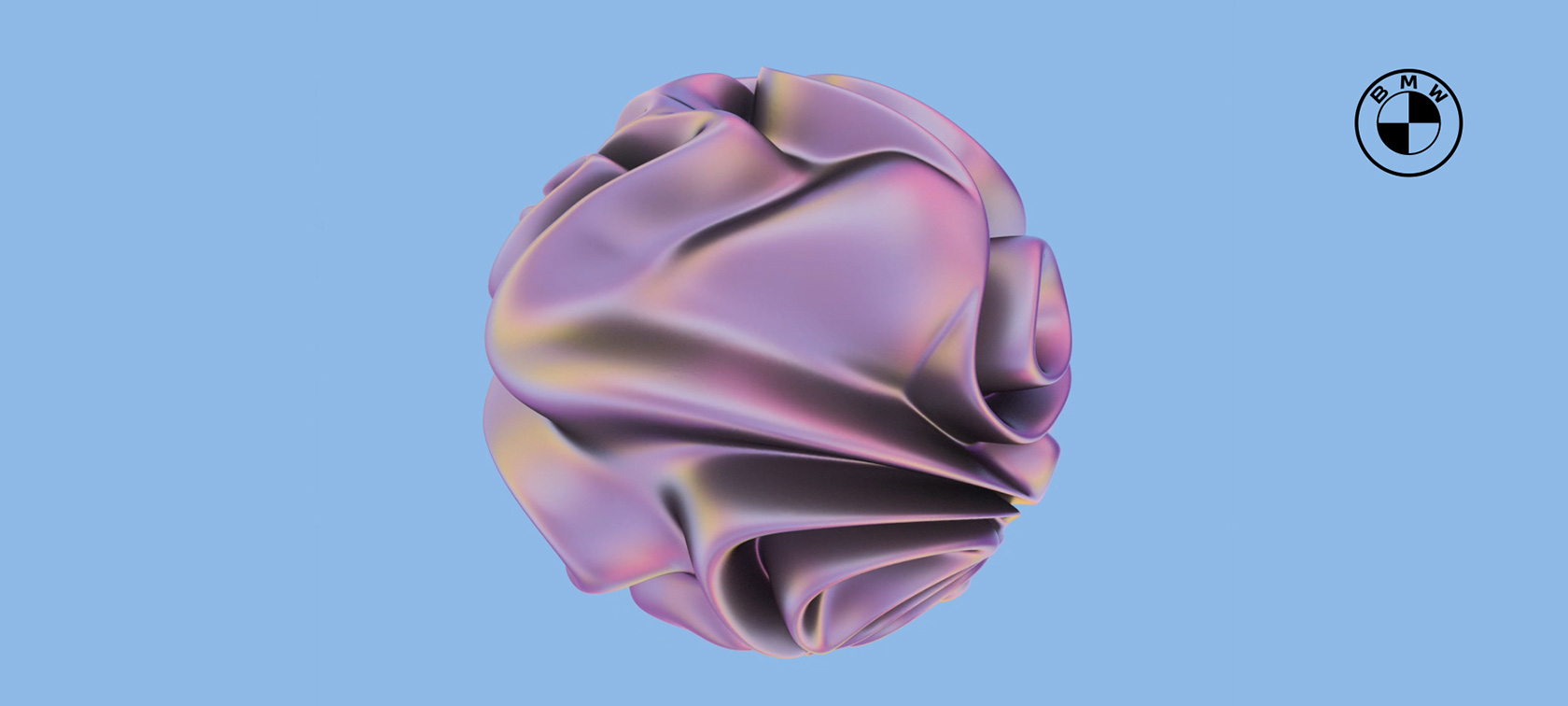
WE GIVE SUSTAINABILITY A FACE.
IN AN EXCHANGE WITH OUR EXPERTS.


Anna is a Specialist for Sustainability Interior and shares her prospects for sustainable materials.
Daniela is Head of Sustainability Design BMW Group and talks about how sustainability affects every decision in design.


MORE BIODIVERSITY THROUGH BEES AT THE SITE.
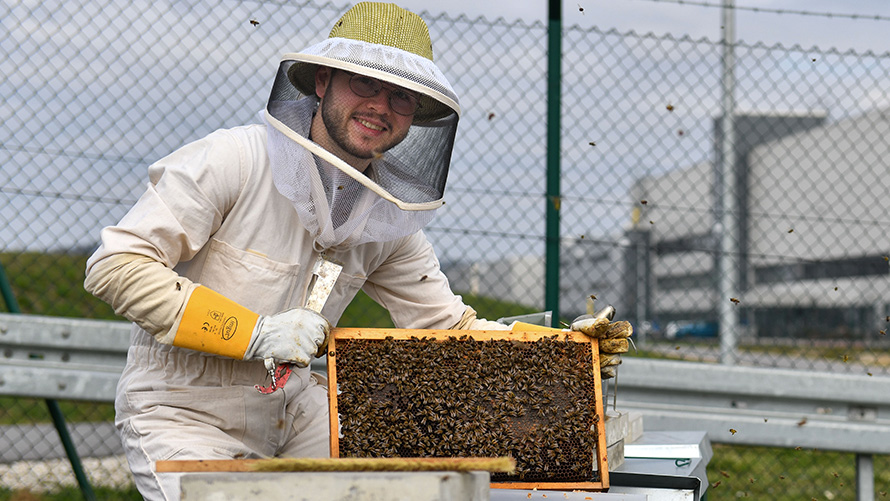
In addition to its consistent sustainability targets, the BMW Group is also joining forces with its employees to pursue many small initiatives aimed at protecting the environment and species. Whether in Munich, Leipzig, Regensburg, Berlin or Dingolfing: various bee species and colonies have found a new home at different BMW Group locations in Germany. The idea originates from employees and provides an important contribution towards more biodiversity.
FREQUENTLY ASKED QUESTIONS ON THE TOPIC OF SOCIAL & GOVERNANCE.
How does the BMW Group practise its social and cultural responsibility?
Commitment to sustainability is part of the philosophy of the BMW Group. As a company with a multinational workforce and locations on five continents, we are part of society and accept our responsibility. We are committed to intercultural communication, well-founded education for children and young adults as well as safety in traffic. The voluntary involvement of our employees makes just as important a contribution to the social responsibility of the BMW Group as does the BMW Foundation Herbert Quandt, an independent company trust.
What sustainable innovations is BMW pursuing?
Through the BMW iFACTORY, the BMW Group is presenting a revolutionary strategy for the automobile production of the future. Implementation of the BMW iFACTORY is taking place in all BMW Group plants around the world. At the same time, it is setting new benchmarks in matters of climate protection and competitiveness with flexible, efficient and digital production technologies. The pioneer project is the new plant in the Hungarian city of Debrecen, which is set to produce the fully electric New Class as from 2025.
How does the BMW Group support diversity?
The BMW Group views diversity as a strength. This is why we use training courses, talks and dialogue formats to create awareness among employees and management staff of the positive contribution that diversity is able to make within the company. Furthermore, the BMW Group promotes diversity and equality of opportunity in personnel development. Key principles such as protection against discrimination, equal treatment for all employees and respect in everyday business are firmly anchored in guidelines, which include the BMW Group Code of Conduct or the BMW Group Code on Human Rights and Working Conditions.
Which social projects does the BMW Group support?
Through its social commitment, the BMW Group aspires to meet specific needs and achieve long-term impact. At the heart of these endeavours, we place projects that we are able to support in a targeted manner through our competencies. At our locations, we develop educational projects aimed at facilitating entry into the labour market for young people and thus opening up better prospects for them in life. In cooperation with the United Nations Alliance of Civilisations (UNAOC), we have been regularly presenting the Intercultural Innovation Award since 2011. The award is bestowed upon projects that seek constructive solutions for intercultural tensions and conflicts.
ELECTRICITY CONSUMPTION AND RANGE.
BMW iX xDrive40:
Energy consumption, combined WLTP in kWh/100 km: 21.2–19.3
Electric range, WLTP in km: 394–426
Official figures for fuel consumption, CO2 emissions, electricity consumption and electric range were determined in accordance with the prescribed measurement procedure and comply with Regulation (EU) 715/2007 as amended. WLTP figures take into account any optional equipment in the case of ranges. For vehicles newly type-approved since 01.01.2021, the official specifications exist only according to WLTP. Further information on the NEDC and WLTP measurement methods can be found at www.bmw.de/wltp
ELECTRICITY CONSUMPTION AND RANGE.
BMW iX xDrive40:
Energy consumption, combined WLTP in kWh/100 km: 21.2–19.3
Electric range, WLTP in km: 394–426
Official figures for fuel consumption, CO2 emissions, electricity consumption and electric range were determined in accordance with the prescribed measurement procedure and comply with Regulation (EU) 715/2007 as amended. WLTP figures take into account any optional equipment in the case of ranges. For vehicles newly type-approved since 01.01.2021, the official specifications exist only according to WLTP. Further information on the NEDC and WLTP measurement methods can be found at www.bmw.de/wltp